The 777X is Boeing’s latest and (theoretically) greatest aircraft, which is eventually supposed to become the largest passenger jet in production. Over 500 of these aircraft have been ordered by over a dozen airlines.
The catch is, the plane has experienced some major certification issues — while the plane was supposed to start commercial service in 2020, that timeline has been pushed back by several years. There’s now at least a little bit of positive news when it comes to the certification process for this aircraft.
In this post:
Boeing 777X test flights resume after engine mount issues
In the summer of 2024, Boeing was aggressively performing test flights with its 777X aircraft, as the aerospace giant worked to get the airplane certified. Unfortunately those test flights came to a halt on August 15, 2024, as a major issue was discovered after a test flight. Specifically, one of the 777-9 test aircraft with the registration code N779XY completed a 5hr31min test flight to and from Kona Airport (KOA).
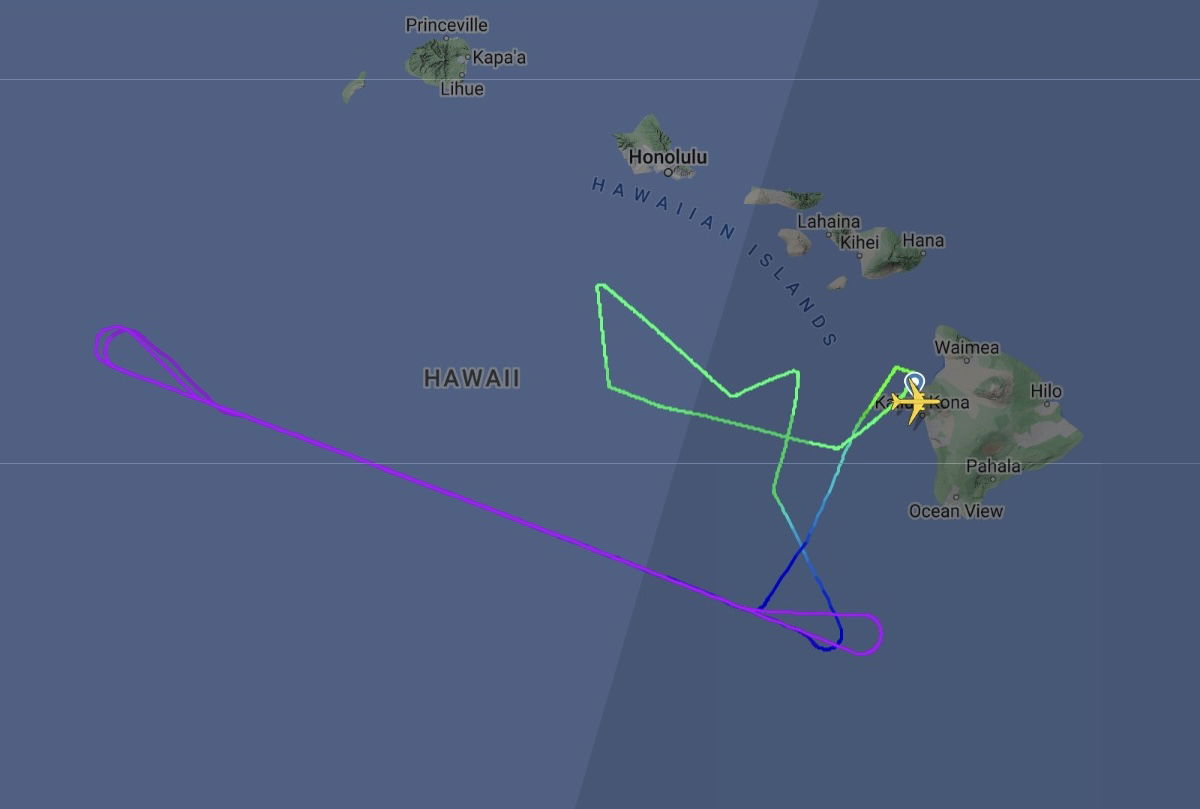
During a routine post-flight inspection, the failure of a crucial piece of structure that mounts the engine of the aircraft was discovered. Upon inspecting the other test aircraft, two other planes were found to have the same cracks, prompting a halt in test flying.
Specifically, the part that had the issue is the thrust link, which is a titanium component that transfers the thrust of the engine to the airframe. This isn’t part of the GE-9X engine that powers the airplane, but rather it’s a component designed by Boeing. Each engine has two of these, for redundancy.
One of the unique things about the 777X is its engines, which are the largest engines on any commercial aircraft. They weigh around 11 tons each, and have a diameter of over 11 feet.
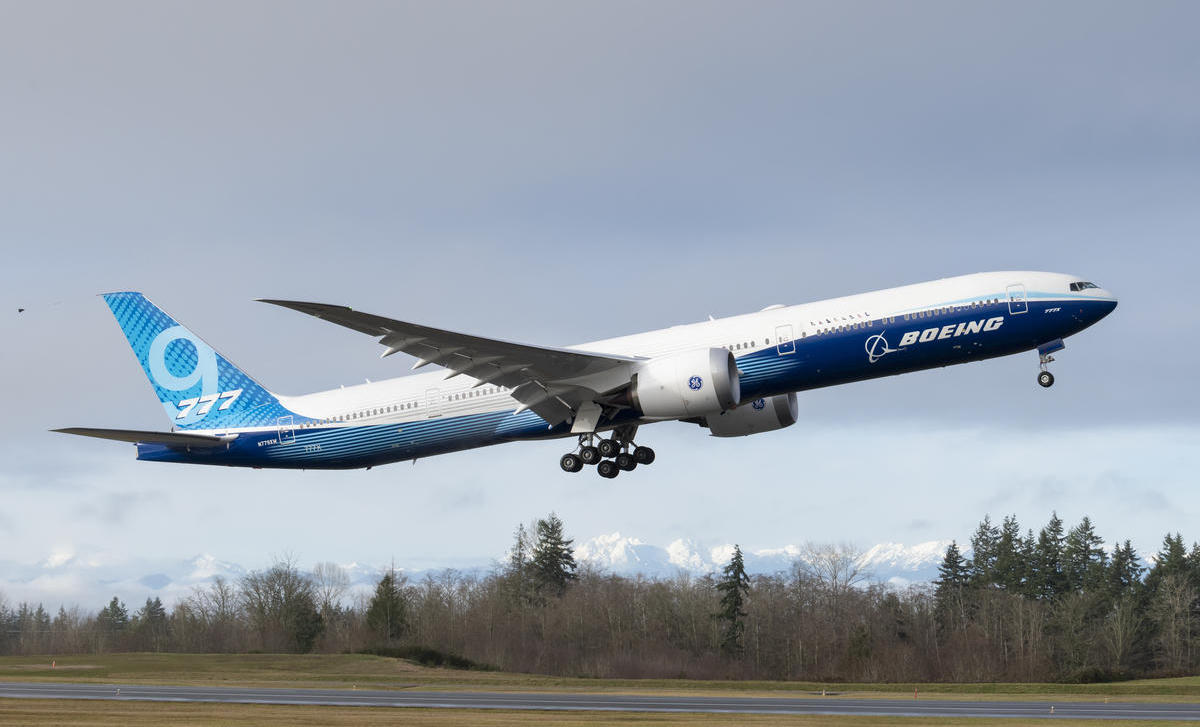
So for over five months, Boeing had paused test flights with its new aircraft, which also pushed back the expected first delivery of the jet from 2025 to 2026.
There’s now a positive update, at least. On January 16, 2025, Boeing resumed 777X test flights. The same exact aircraft that operated the test flight in August 2024, operated a 2hr11min test flight to and from Boeing Field Airport (BFI).
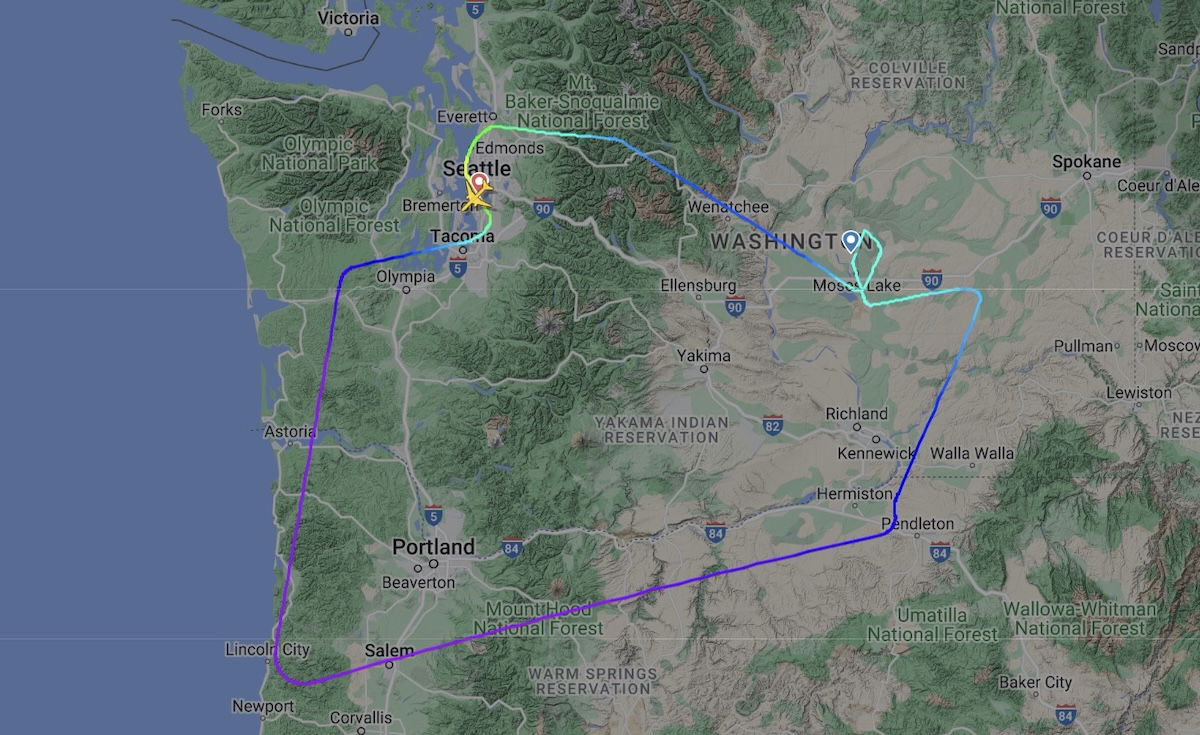
Let’s hope the 777X enters service in 2026
Of course aircraft manufacturers perform extensive test flights for good reason, to work out any kinks or issues before the planes enter service. First and foremost, this is about safety. But on top of that, it’s less costly to discover issues before aircraft are mass produced and in service.
Given Boeing’s history, the focus needs to be on doing things slowly and correctly, rather than speeding through things. However, I think it goes without saying that airlines are desperately hoping that the testing goes smoothly from hereon out, and that certification of the jet happens some time in 2025.
With the latest pause in testing, the delivery timeline for the first 777X was pushed from 2025 to 2026. Many airlines are relying on Boeing’s ability to get this jet certificate in order to be able to execute their fleet plans, since Boeing has been having delivery delays with just about all of its aircraft.
For passengers, the Boeing 777X is a really exciting plane, given that many airlines plan to introduce new cabin concepts on these aircraft. Airlines like Cathay Pacific, Emirates, Qatar Airways, etc., are all desperate to add these planes to their fleet.
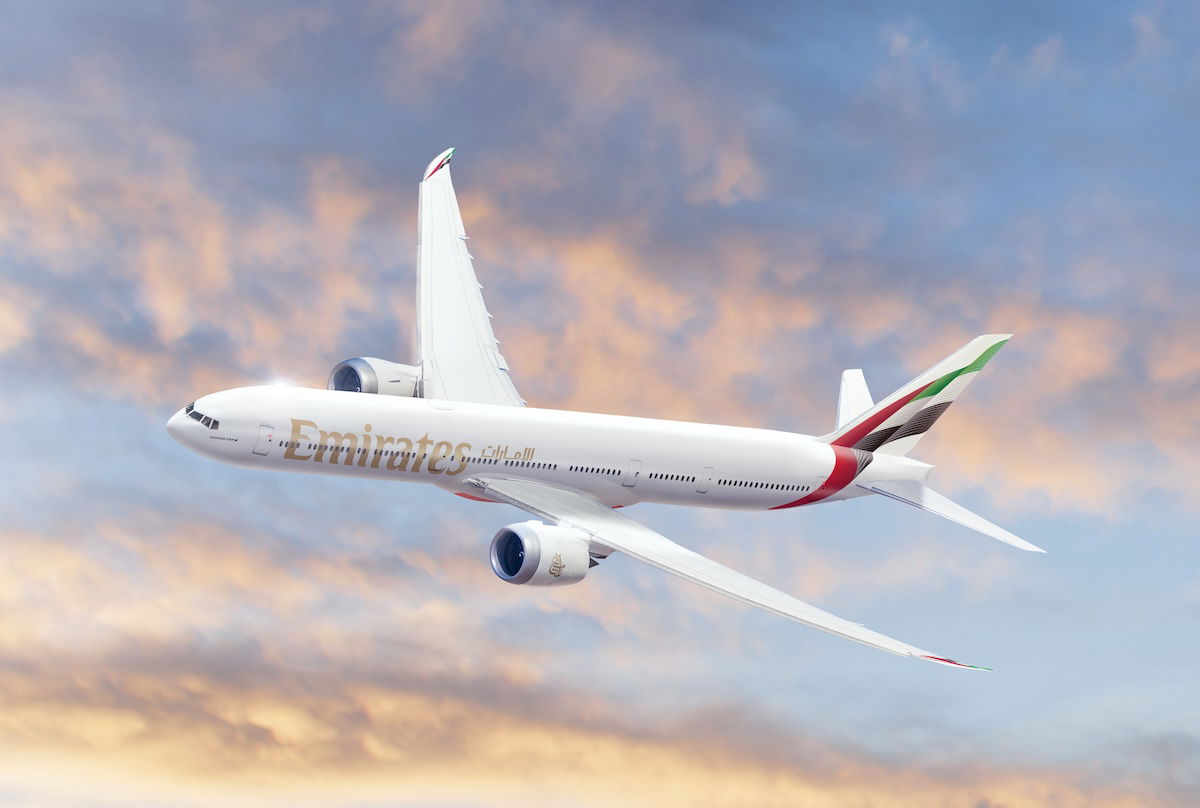
Bottom line
In August 2024, the Boeing 777X certification process faced a major setback, when test flights had to be paused. Over five months later, we’ve finally seen these flights resume, which is a positive development. The 777X is now expected to be delivered to airlines as of early 2026. For the sake of passengers, airline customers, and Boeing, I hope that timeline sticks.
When do you think the Boeing 777X will actually enter service?
Is the 777X program being managed by the same people who built the Berlin airport or the Majesty Building in Florida?
Sorry to interrupt the lovely Boeing Vs Airbus discussion, but does anyone know why they chose to call it 777X? Given the amount of new engineering that went into it, and the fact that the 777 is nearly 30 years old, I thought 797 would be cooler. Or are they scared they will run out of model numbers? Or is there a 797 already in the works? Interested in both the aviation aspect and the marketing angle - all answers are appreciated
Pilot certification will largely carry over from the 777. More hurdles to clear with a new line of aircraft.
It's also widely believed that 797 has already been "reserved" for a new generation of midsize aircraft (e.g. to replace aging 767s).
777X is just the development name for that series of aircraft. The actual aircraft will be the 777-8 and 777-9, in line with Boeing's new numbering system introduced with the 787. Like the 787-8/9/10, 747-8, and 737 MAX-7/8/9/10.
Manufacturers rarely completely change their model numbering for upgrades these days since they want to emphasize commonality with existing aircraft for cost and certification reasons. Boeing has of course kept the same numbering for the 737 and...
777X is just the development name for that series of aircraft. The actual aircraft will be the 777-8 and 777-9, in line with Boeing's new numbering system introduced with the 787. Like the 787-8/9/10, 747-8, and 737 MAX-7/8/9/10.
Manufacturers rarely completely change their model numbering for upgrades these days since they want to emphasize commonality with existing aircraft for cost and certification reasons. Boeing has of course kept the same numbering for the 737 and 747 family since the 1960s, and Airbus did the same with the A320neo and A330neo series.
Boeing is doing the right thing. Yes they continue to be the whipping boy for the media. I’m surprised the thrust link fix wasn’t fast tracked like the 787 battery issue. They’ve fixed it now, and a speedy cert should be the result. Looking forward to flying on a new 777X
One is amused at your apparent trust in Boeing at this time.
Personally, I am looking forward to the day when I am free to choose only Airbus commercial aircraft flights. Those being primarily A350 and A380 for my future international flights …. I do so enjoy these aircraft.
I've taken no less than 20 A350XWB flights the past 3 years (all on QR and will be trying it on CX next month). It's a phenomenal plane no doubt however to say it's THE BEST plane in town and hoping for the competition to fail is...not really smart.
I've flown on the A380 a few times as well. Great plane too.
That being said, A LOT of how "comfortable" a plane is depends...
I've taken no less than 20 A350XWB flights the past 3 years (all on QR and will be trying it on CX next month). It's a phenomenal plane no doubt however to say it's THE BEST plane in town and hoping for the competition to fail is...not really smart.
I've flown on the A380 a few times as well. Great plane too.
That being said, A LOT of how "comfortable" a plane is depends on the carrier, not the plane. Yesterday I flew on two Air Arabia flights. One was an A320NEO and another was an A321CEO. The A321CEO in terms of comfortability wasn't even close to the A320NEO.
Finally, you think Airbus will innovate if they have no competitors?
Give me an Airbus A350 any day, which is a dream to fly in. They're built by engineers who also care about passenger comfort.
Boeing's new planes are built by bean counters who care about cutting costs and who market lies.
When comparing the A350 to the 787 introduction, there is no comparison. The A350 has had extremely high dispatch reliability, while the 787 not only spontaneously combusted and had to the grounded by...
Give me an Airbus A350 any day, which is a dream to fly in. They're built by engineers who also care about passenger comfort.
Boeing's new planes are built by bean counters who care about cutting costs and who market lies.
When comparing the A350 to the 787 introduction, there is no comparison. The A350 has had extremely high dispatch reliability, while the 787 not only spontaneously combusted and had to the grounded by the regulators, but it still has a lower dispatch reliability after all these years. And 787s are just way too narrow, and those cost-savings window screens are absolutely awful and detract from the joy of flying (especially Boeing's decision to allow crew to lock them - once again, at design choice that's not passenger-centric)
No thanks.
Question Jack, if I may?
On a scale of: 1 to 10. (1 being the least likely).
What is the likelihood of getting the truth of the situation from Boeing?
Also, how trustworthy will the Boeing answers be?
Perhaps someone else might have a view too?
Truth our of Boeing? 1.
I also still own stock...
Thank you Bear, likewise there are Boeing shares in my portfolio too …. does that make me a hypocrite?
@AeroB13a
No, that doesn't make you a hypocrite.
Specifically YOU.
You're already a hypocrite anyways.
There's more than enough things that make you a hypocrite.
Thank you so much for your kind words Eskimo fanboy.
One much prefers to receive an attempt to be insulted rather than to be ignored.
When you look at the accident/incident history of both Airbus and Boeing, the vast majority of events are attributable to a human failure as opposed to a design failure. Armchair quarterbacks will say what they will but I'd rather wait for a right answer than rush a wrong answer.
Well yes, everything made by humans that fails is ultimately human failure; this is not very helpful.
But 787s catching fire on their own in the air is not the fault of anyone else but Boeing's humans.
Humans are well known to be unreliable but in most industries are unavoidable. Technology is designed to provide a safety net. When it fails to do so, it is a design failure.
The canonical example from the IT world is the intern accidentally dropping the production database. Don't blame the intern for making a dumb mistake; blame the system that allowed an intern root access in the first place.
Besides the 737MAX-7 and MAX-10, has there been any other airliner that had so much time between the first flight and certification?
The original 777, the 787, the A330 and A350 all had 10-24 months between first flight and certification, the 777-200 being very fast.
The 777X will "celebrate" 5 years after their first flight next week (25 Jan); are there other examples in history?
I am quite prepared to be corrected on the following observations, however, it is my understanding that Boeing have tried to “puff out” the fuselage of the old triple 7, beef up the wings and hang larger engines from them.
The results, redesign of many fuselage components, suspect composite wing which needed another redesign and due to the wingspan being too wide, folding tips had to be ‘nailed’ on.
It all sounds very...
I am quite prepared to be corrected on the following observations, however, it is my understanding that Boeing have tried to “puff out” the fuselage of the old triple 7, beef up the wings and hang larger engines from them.
The results, redesign of many fuselage components, suspect composite wing which needed another redesign and due to the wingspan being too wide, folding tips had to be ‘nailed’ on.
It all sounds very Heath Robinson to the casual observer. Development engineering by MBA and bean counter management, rather than Certified Aeronautical Engineers.
Those changes, "beefing up the wings and hanging larger engines," are standard for pretty much every re-engined model on the market. Airbus and Boeing have both done it on most of their models (bar the very newest ones like the A350 and 787, or less successful ones like the A380). There's not really anything new there. Not sure what you mean by "puff out the fuselage." AFAIK the external diameter is the same, they just...
Those changes, "beefing up the wings and hanging larger engines," are standard for pretty much every re-engined model on the market. Airbus and Boeing have both done it on most of their models (bar the very newest ones like the A350 and 787, or less successful ones like the A380). There's not really anything new there. Not sure what you mean by "puff out the fuselage." AFAIK the external diameter is the same, they just slightly thinned the gap between the internal and external walls to expand the cabin space by a few inches.
Folding wingtips were always going to be necessary. The existing 777-300ER is just 0.2 meters from going into Code F alongside the A380 and 747-8 so there's virtually no room for improvement without a folding tip, especially now that research has proven that flatter wingtip devices like sharklets, blended winglets, and raked wingtips are more aerodynamically efficient than the old vertical wingtip fences. No one wants to end up like the A380. FWIW, as far as I know the folding wingtips haven't been a significant contributor to the delays.
The delays are troubling about what they say about some of Boeing's internal processes, but the basic concept for the modernization isn't new. Bigger engines (along with related reinforcement to the wings) and refinements to wing efficiency. A tried and true recipe, it's just that a new solution was required for the wings due to gate restrictions.
Boeing took the 747 classic, redesigned the flight deck so drastically to the point it is unrecognizable to the original, put a brand new wing on it, put brand new engines on it and built one of the most successful airliners in history, the 747-400.
I anticipate more orders once it goes into service. I can see Air France, EVA as likely customers. But it would be nice to see a completely new customer for the 777 aside from Lufthansa. Unfortunately there's no new customer left that needs an aircraft of that size!
Those airlines with sense will buy AirBus as …. ‘if it’s Boeing it ain’t going’ …. who’s living dangerously today with the devil in him?