On January 5, 2024, an Alaska Airlines Boeing 737 MAX 9 made global headlines, when a door plug blew off while the aircraft was inflight. This caused the FAA to temporarily ground the Boeing 737 MAX 9, so that regulators could investigate what happened. The jet is now flying again, but with updated inspection guidelines.
Given the Boeing 737 MAX’s history, there have been a lot of questions about what caused this incident. At first we wondered if there was a bigger issue with the 737 MAX 9, or what could cause a door just blow off while inflight?
Well, the National Transportation Safety Board (NTSB) has just published its preliminary findings regarding this incident, and the cause is exactly what had been rumored in recent weeks.
In this post:
Boeing forgot to install bolts on 737 MAX 9 door plug
While it’s worth reading the entire 19-page NTSB report about what happened, let me summarized what caused this incident:
- Spirit AeroSystems manufactures the fuselage of the 737 MAX 9; the door plug was manufactured in Malaysia on March 24, 2023, and was sent to Spirit AeroSystems’ Wichita facility on May 10, 2023
- The door plug was installed and rigged on the fuselage, and then shipped to Boeing on August 20, 2023, arriving at Boeing’s Renton facility on August 31, 2023
- On September 1, 2023, records show that a report was written about five damaged rivets on the edge frame forward of the left door plug; in order to repair this, four bolts had to be removed from the door plug
- The rivets were repaired correctly, but then the door plug was re-installed without the four bolts, which is obviously the major issue that caused this mess
- The NTSB notes that “the investigation continues to determine what manufacturing documents were used to authorize the opening and closing of the left MED plug during the rivet rework”
Even at this point, Boeing hasn’t been able to provide any documentation about who opened and closed the door plug, how it was done, and with what authorization. While this isn’t contained in the NTSB report, a whistleblower previously claimed that this slipped through the cracks because Boeing has a process failure whereby it uses two separate systems to record what work has been completed.
The systems obviously aren’t in sync, and that’s what caused this. Still, one has to wonder if the people putting the door plug back on without bolts knew something wasn’t right, or if this is such an easy mistake to make?
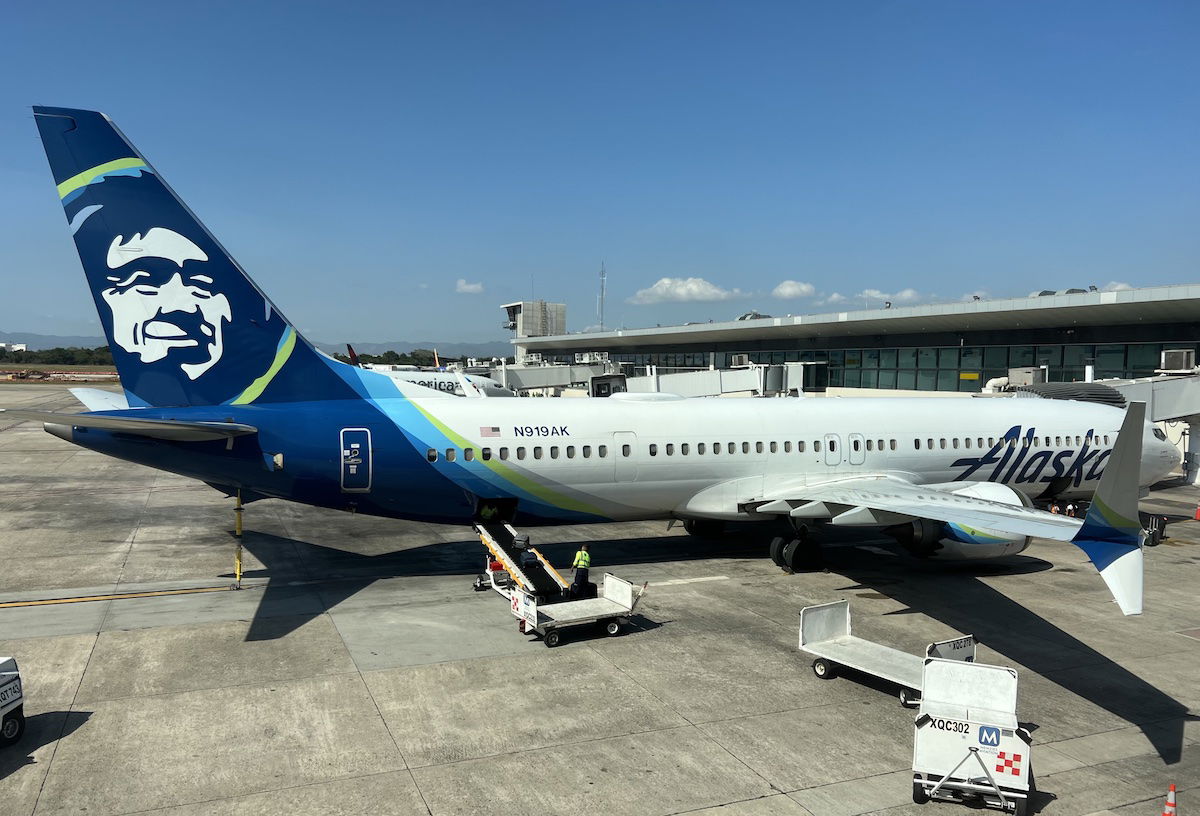
I’m not sure if this is a good or bad update
On the one hand, I suppose it’s good news that there’s not actually an additional, consistent problem with the 737 MAX, but rather there was an error that can easily be traced.
On the other hand, how the heck does an aircraft manufacturer have a process in place whereby a repair is performed, four bolts are missing, and there are no quality control measures in place? Even a month after the incident, Boeing still doesn’t know who performed this repair work?
How is that even remotely excusable for a company that is the United States’ largest exporter, and which has been producing planes for decades? And how is it possible that this is the process after Boeing got so much scrutiny regarding the 737 MAX, after it was grounded for nearly a couple of years?
There are still quite a few questions, though, even beyond accountability surrounding who installed this door. For example, 737 MAX 9 operators performed inspections on aircraft following the incident in recent weeks, and many found loose bolts. Are those loose bolts normal, since that seems to be different than this situation, where the plane was just missing four bolts?
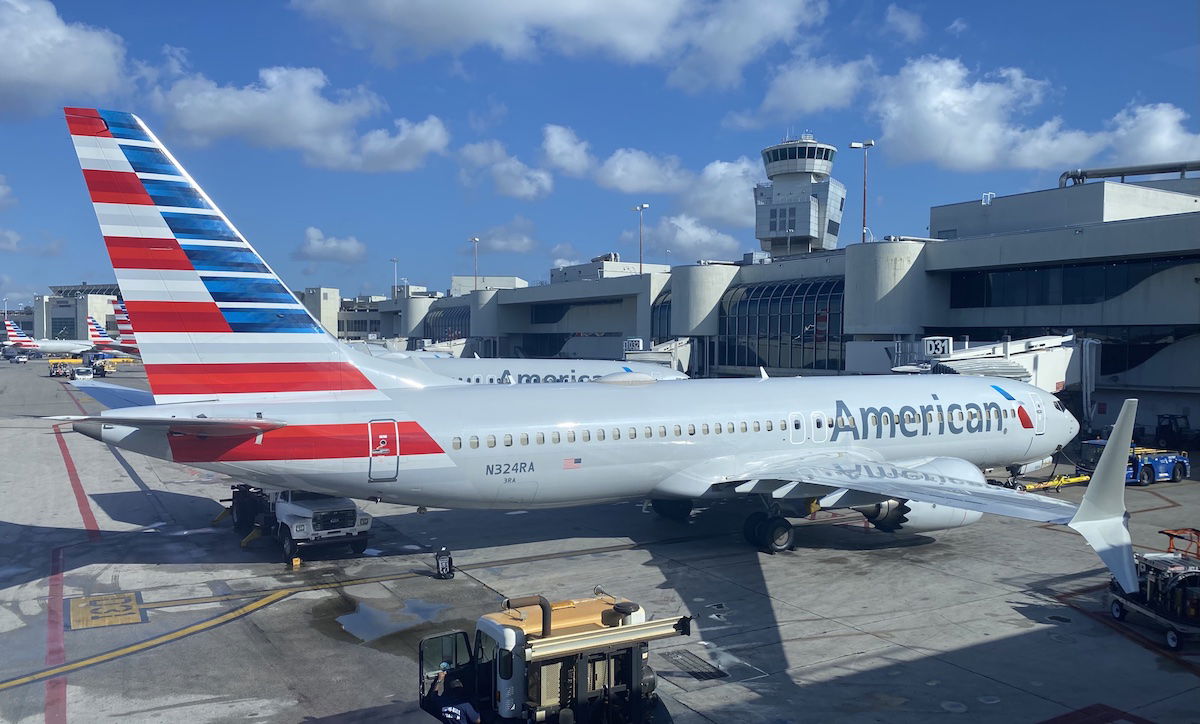
Bottom line
The NTSB has now released its preliminary report into the Alaska Boeing 737 MAX 9 incident, where a door plug blew out. We now know that when the fuselage of this particular jet was sent from Spirit AeroSystems to Boeing, there was an issue with some of the rivets that required a repair.
The repair required removing a door plug (and four bolts), but somehow the people performing the work forgot to install the bolts once the work was complete. While there are supposed to be quality checks in place, those just didn’t happen, as it seems that Boeing has a bit of a paperwork issue.
I can’t decide if it’s reassuring to think that there’s not a bigger issue with the aircraft, or terrifying to think that Boeing’s quality control is so poor.
What do you make about the preliminary NTSB report about the 737 MAX 9 incident?
People can talk as much as they want about the four missed bolts. But something which, as far as I have seen, fails to ever get mentioned is the incredibly impressive 99.9% success rate of Boeing aircraft coming off these very same production lines. Thousands of people work very hard to deliver a reliable product and it's an amazing feat of cooperation and human ingenuity that this is even possible.
Shit happens, people make mistakes....
People can talk as much as they want about the four missed bolts. But something which, as far as I have seen, fails to ever get mentioned is the incredibly impressive 99.9% success rate of Boeing aircraft coming off these very same production lines. Thousands of people work very hard to deliver a reliable product and it's an amazing feat of cooperation and human ingenuity that this is even possible.
Shit happens, people make mistakes. Are there places to improve? Always. Are the profiteering attitudes of Boeing management the right way to run a business? Absolutely not. But let's not forget the millions of Boeing flights which have had zero issues, the hundreds of thousands of Boeing planes which have flown successfully (often even beyond their intended service life), and the tens of thousands of people that go to work every day to make this all happen.
How could the plug, without the 4 restraining bolts c/w castle nuts and cotter pins, during several flights over a period of not less than 40 days, some of which encounted heavy turbulence along with internal and external forces acting on or against it, remain in place? On the incident flight, could an internal differential force acting against the plug window (at 14,840 feet elevation) have been enough to cause the stop plug pins to...
How could the plug, without the 4 restraining bolts c/w castle nuts and cotter pins, during several flights over a period of not less than 40 days, some of which encounted heavy turbulence along with internal and external forces acting on or against it, remain in place? On the incident flight, could an internal differential force acting against the plug window (at 14,840 feet elevation) have been enough to cause the stop plug pins to free themselves allowing the now boltless fittings to fail? My thoughts only. Tog
There’s a deeper reason that many people don’t want to admit that’s going on. I wonder how many people weren’t hired based on their actual qualifications....
You never know when parts will fall off a Boeing.
Fly Boeing at your peril. Terrible company and terrible products. If it’s Boeing ain’t nobody going.
To play the devil's advocate a bit.
And how is it possible that this is the process after Boeing got so much scrutiny regarding the 737 MAX, after it was grounded for nearly a couple of years?
Because the issues of the MCAS had nothing to do with production process and quality assurance on the line.
That's exactly the concerning part. If there are two fundamental failures, so far detached that investigating one does not reveal the other, the door opens to there being a third, fourth, or tenth.
Lego (or insert here any other building toy) 101 - why do we have four bolts left over?
My dad used to work for Boeing on the 737 line in Renton back in the 90s. He was constantly complaining that management would be on his case for going too slow. They wanted him to work faster, which he argued (rightfully) that the faster they make them go, the more chances there are to make a mistake. He would always say 'no one is in that much of a hurry to die, so why...
My dad used to work for Boeing on the 737 line in Renton back in the 90s. He was constantly complaining that management would be on his case for going too slow. They wanted him to work faster, which he argued (rightfully) that the faster they make them go, the more chances there are to make a mistake. He would always say 'no one is in that much of a hurry to die, so why should I go faster? It takes me as long as it takes me to do the job right.' It seems to me that nothing has changed in the last 30 years, and in reality has probably gotten worse. As the daughter of a Boeing man I used to always prefer to fly Boeing, but over the last several years I find that I will go out of my way to fly Airbus when possible and I don't see that changing any time soon.
Too bad they can't lure Alan Mulally back to right the Boeing ship.
Realistically, what would/could he even do?
Boeing's fundamental problem is that it went from being a company run by engineers who climbed through the ranks, therefor knowing what it takes to craft a quality aircraft in-house...
...to Jack Welch acolytes, who wanted to run a Wall Street lobby that coincidentally snaps together pre-fabricated parts for aircraft models well past their prime, as its seed-money scheme.
And then stayed that way for the last quarter century.
...Realistically, what would/could he even do?
Boeing's fundamental problem is that it went from being a company run by engineers who climbed through the ranks, therefor knowing what it takes to craft a quality aircraft in-house...
...to Jack Welch acolytes, who wanted to run a Wall Street lobby that coincidentally snaps together pre-fabricated parts for aircraft models well past their prime, as its seed-money scheme.
And then stayed that way for the last quarter century.
One person, no matter how potent, would really struggle to change that, after all this time. :(
Manufacturing quality in Renton has been going down the tubes for years now. So what’s Boeing’s response? Move HQ back there from distant Chicago?
Nope. They’re moving to DC instead, even further from the manufacturing HQ. They’d rather be closer to the politicians than their assembly line. Why try and fix defects when you can just lobby them away? Disgusting.
"Why try and fix defects when you can just lobby them away?"
And they're certainly trying, too. They just applied for a safety exemption on the MAX7 and MAX10, rather than fix the problem through engineering (imagine such a thing) a redesign.
Then on top of that, they move production to what's arguably scab labor, in S.Carolina.
Hope 3 production shutdowns in only 2 years, due to QC issues on the 787, was worth it.
Keep firing experienced technicians, reduce spending in quality control, use that money for stock buybacks, increase CEO and shareholder payout.
This is in essentially what all corporations are doing.
Only thing, Boeing's products have to stay up in the air.
And you can argue with techs, argue with stockholders, argue with the FAA, even argue with laws passed by Congress..... but the thing you cannot argue (or even bargain/compromise) with, are the laws of physics.
Yet Boeing sometimes seems intent on doing just that.
On December 6, 2012, Washington became the first U.S. state to legalize recreational use of marijuana and the first to allow recreational marijuana sales. That said, Boeing employees are subject to random drug testing with the company doing 5 panel drug test on new employees and random tests if accidents occur. Any other former aerospace workers wondering if this epic failure by employees in repair and quality inspection qualifies as an accident?
The problem isn't cannabis, it's unfettered capitalism.
Really because total socialism is a total failure.
Why do you see that as some kind of defense against the notion of unfettered capitalism/corporatism?
Did you ever consider the possibility of, say, neither being an optimal state of operation.....?
You realize that corporate drug testing has been a thing for decades on end, and didn't just cease when marijuana became legal on a state level, right?
The FDA will still perform random drug tests along with Boeing.
It sure makes you wonder what else might be mis-installed on the plane.